Integrated Zinc Die Casting and CNC Machining Solutions
Integrated Zinc Die Casting and CNC Machining Solutions
Blog Article
As robotics and intelligent equipment advance, transmission components like precision gear housings and servo motor shells must achieve unprecedented levels of strength and accuracy. Traditional aluminum machining often falls short, driving up costs and lead times. Junyin’s integrated solution leverages the advantages of zinc die casting with post‐processing precision to deliver high‐performance parts that meet the rigorous demands of today’s automation industry.
Why Choose Zinc Die Casting for Structural Housings?
Zinc alloys such as AZ91D offer a compelling alternative to aluminum: superior tensile strength (≥380 MPa), excellent dimensional stability, and superior castability for complex geometries. By partnering with a dedicated zinc die casting mold manufacturer, Junyin produces housings with integrated ribs, cooling fins, and thin‐wall sections in a single molding operation—dramatically reducing material waste and eliminating secondary assembly steps.
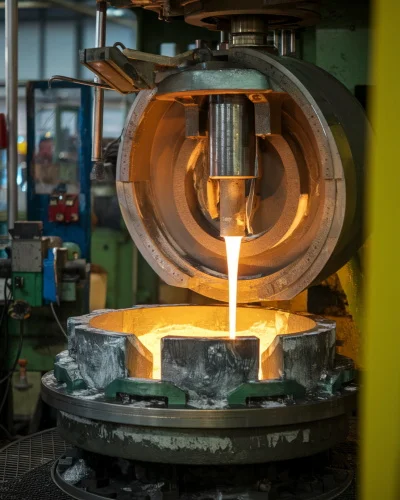
Case Study: Harmonic Reducer Housing for Collaborative Robots
A leading cobot manufacturer needed a harmonics reducer housing with in‐built stiffening webs and precise gear mounting bores. Junyin designed and produced the zinc die casting mold, optimizing flow channels and cooling circuits using advanced mold flow analysis. The result: a defect‐free housing cast in under 30 seconds with surface roughness controlled below Ra1.6, ensuring minimal machining allowance.
Achieving Micron‐Level Accuracy with CNC Machining
After casting, each housing undergoes precision finishing on Junyin’s five‐axis machining centers. Critical gear bores are bored to a circularity tolerance of 0.008 mm, while integrated lubrication channels—2 mm in diameter and 50 mm deep—are drilled using specialized deep‐hole drilling tools. This seamless handoff from casting to milling is only possible with an in‐house CNC machining service partner, ensuring tight control over all process variables.
Thermal and Mechanical Treatment for Enhanced Performance
To further improve mechanical properties, cast housings undergo T6 heat treatment, elevating fatigue resistance and dimensional stability. This step is critical for parts subjected to dynamic loads in servo drives and gearboxes. Junyin’s engineers monitor temperature profiles closely to prevent over‑aging and ensure uniform hardness throughout the component.
Surface Integrity and Deburring Excellence
After machining, parts are vibratory‐deburred to remove flash and sharp edges without altering tolerances. A passivation treatment then enhances corrosion resistance, vital for long‐term reliability in factory automation environments. Final surface roughness meets the stringent requirements of gearbox assembly, reducing seal wear and prolonging service life.
100% Inspection and Quality Assurance
No part leaves Junyin’s facility without full dimensional verification on a coordinate measuring machine (CMM). Every critical feature—bore position, hole size, and flatness—is checked against the digital drawing. With a 100% pass rate on key tolerances, customers gain confidence in assembly fit and function. Detailed inspection reports accompany each shipment, supporting traceability and compliance with international standards.
Cost Reduction and Lead Time Compression
By integrating zinc die casting mold manufacture with precision CNC machining, Junyin cuts total manufacturing costs by up to 25% compared to all‑machined aluminum housings. Lead times shrink from 6–8 weeks to just 3–4 weeks, enabling rapid iterations and quicker time‑to‑market for new automation equipment.
Collaborating with Industry Leaders
Major robotics OEMs and industrial automation suppliers—companies like Rockwell Automation—trust Junyin’s expertise for mission‑critical components. By aligning material selection, process design, and precision finishing, Junyin helps these leaders maintain innovation momentum while upholding the highest quality standards.
Sustainability and Material Efficiency
Zinc alloy recycling and minimal machining waste position Junyin’s process as an eco‑friendly alternative. Scrap metal from die casting is re‑melted on‑site, and machining chips are collected for recycling, reducing environmental impact and supporting clients’ sustainability goals.
How to Get Started with Junyin’s Solutions
Ready to elevate your transmission component design with high‑strength zinc die casting and precision CNC machining? Contact Junyin for a free feasibility study and quotation. Benefit from end‑to‑end support: mold design, casting, heat treatment, multi‑axis machining, surface finishing, and quality assurance—all under one roof.
Explore our services: